Quality performs well
The plasma cutting system manufacturer Elettro C.F. is delivering a metal-cutting quality that has never been reached before thanks to HANDYSURF+ from ACCRETECH.
Elettro C.F., a manufacturer of plasma cutting systems, has patented an innovative system for achieving high-quality cuts through the synergy of different processing parameters. Mobile measurement with the HANDYSURF+ surface measuring device allows the quality of the cut surface to be precision-controlled under various conditions and configurations
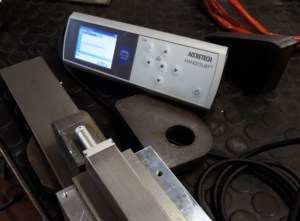
Measuring the quality of the cut surfface with the roughness measurement device Handysurf+. © Elettro C.F.
The Italian company Elettro C.F. has been developing generators for electric arc welding and plasma cutting for almost 50 years. With plasma cutting, a plasma jet – in other words, ionised gas – is used as a source of heat at extremely high speeds and temperatures. Plasma allows steel and other metals to be cut quickly and cleanly. The Synergic Plasma system, which was patented by Elettro C.F. in 2019, allows a standard of quality that has never been reached before with a conventional plasma cutting system.
“Today, our products are able to carry out cleaner, better-quality cuts by influencing the physical, mechanical and structural properties of the components that form part of the cutting lance”, said “Various specific nozzles for different types of processing can be mounted onto a plasma burner. These can then influence the properties of the plasma and therefore the quality of the surface.”
Since the cutting result depends on several different variables, the focus of Elettro C.F.’s research and development activities has been on identifying the best combinations of processing parameters and the development of new components. For each configuration, cutting trials are therefore carried out with different parameters and the quality of the surface measured.
Higher cut quality requires objective evaluation parameters
“The increase in quality has made it almost impossible to distinguish between the various tests with the naked eye. Therefore we needed a measuring device that could precisely check the quality of the cuts under various conditions and configurations”, continued Castaldi. These requirements prompted Elettro C.F. to look for an instrument capable of precisely evaluating the cut surface. It was also important that the device can be moved directly to the cutting site and used easily, even with especially bulky components.

Fabrizio Castadi, Technology Director at Elettro C.F. © Elettro C.F
Starting with a reading of the ISO parameters, which define the specific roughness values for high-quality cuts, Castaldi carried out market research at the start of 2019. After evaluating several solutions available on the market, Castaldi chose a solution from ACCRETECH.
“I had never used a roughness measuring device before, so I didn’t really know what sort of instrument I was supposed to be looking for. I contacted all of the major manufacturers of surface measuring devices and ACCRETECH offered me the most impressive solution, as well as offering to come and carry out a product test on-site.”
Elettro C.F. was impressed by the range of portable HANDYSURF+roughness measuring devices, which allow measurements to be carried out quickly, easily and accurately even directly in production. The display with its extremely intuitive navigation menu allows every member of the production team to manage important surface parameters without having any specialist measuring expertise.
“In addition to excellent agility and ease of use, HANDYSURF+ also offered fantastic additional functions such as the option of connecting it to a PC, and the software included in the scope of delivery which turns it into a small mobile measuring station featuring everything we needed”, explained Castaldi. “The ACCRETECH team also showed me the application in no time at all. We carried out the tests together, and it was all this that sealed the deal for us – as well as the fact that the configuration we chose also represented the best price compared to the competition.”
With the introduction of the portable HANDYSURF+ roughness measuring device, it has become much simpler for Elettro C.F. to determine the ideal configuration for the best results. The reference parameter for the tests is the average roughness (Ra). To put it more precisely, employees detect fluctuations in roughness on the cut surface if individual variables change.
“These days, we make minimal changes during our product tests that lead to improvements which are becoming increasingly small compared to the standards. Without a practical and precise instrument for certifying the results achieved, these improvements would not have been possible”, continued Castaldi. “Even the tiniest deviations are of major importance, especially since they enable us to immediately understand whether we are moving in the right direction.”
When a measuring device becomes a commercial resource
With the roughness measuring device, Elettro is able to demonstrate the higher quality of its cutting systems to the outside world based on objective data, allowing it to stand out from the competition both at home and abroad.
Quality awareness is also changing on the plasma cutting market since ultimately better cutting quality reduces the need for further processing and therefore costs. The significant improvement in quality means that Elettro can in future maintain its presence on a market that makes ever-stricter demands.
Measuring results for targeted use in customer advice
Apart from the laboratory tests, it was also important that customers are able to directly notice the improvement in cut quality for their specific applications. Even if synergetic plasma cutting systems control their operating parameters themselves, multiple variables depend on the user and the movement systems.
Elettro C.F. assists its customers during the plasma cutting assembly stage on workbenches and provides its own software so that the entire system can be correctly set up for the type of processing in question as a function of the thickness, material type, cut dimensions and operating factors.
During this phase, the use of the portable ACCRETECH HANDYSURF+ roughness measuring device allows the customer to directly check the results. The test can be carried out at the customer’s premises or Elettro C.F.’s plants.
The on-site tests play a key role in impressing the customer, as Castaldi confirms: “The cutting quality of our systems allows us to achieve a level of quality comparable with that of significantly more expensive technologies, meaning that many customers are confused. Therefore the measurement of results with the customer is an irrefutable test that helps to overcome even the strongest resistance.”
About ACCRETECH
ACCRETECH was founded in Tokyo in 1949 and is now one of the world’s leading providers of products for precision measuring equipment and of the most modern equipment for the semiconductor industry. ACCRETECH has been established on the European market since 1989 and now benefits from a comprehensive sales and service network.